quality control
Our quality control consists of 21 elements:
1. Certification to ISO 9001
We manage our quality-system according to ISO 9001-2008, which was certified for all locations.
For the production of series-parts in Gottmadingen we work additionally to the quality standards of TS 16949, and VDA 6.2
2. Customer-audits
Our large customers have also audited us to their own quality standards, that are special for
specific processes and products.
3. CMMs in quality room
We run calibrated coordinate-measurement-machines (CMM) at all locations. Large parts for the machine-tool-industry can be
measured best on a large handguided Stiefelmayer-machine with a table size of 5 meters. Series-parts can be measured best
automatically on a large NC-controlled Zeiss-machine with a table-size of 5m (UMC 850). Thus we can establish in-house the
complete documentation for first-article-inspection (FAI).
4. Mobile control-arm Faro
For mobile applications, especially for the assembly of large machines and installations, we work with a Faro control-arm.
5. Theodolite
Measurements of long distances are taken by a theodolite.
6. Calibrated milling machines and DKD-furnaces
BAll measurement-systems shall be checked regularly for correctness, as a regular part of the ISO 9001 routine. We go 2
steps further:
- our NC-milling-machines are regularly checked and tuned by outside specialists
- our furnaces work with controllers and temperature displays that have been calibrated by the official DKD-service Deutscher Kalibrier-Dienst).
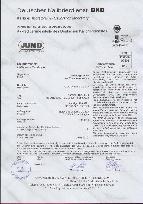
7. Welding permits, even for aluminium and stainless steel
All welders work with active welding permits. For the welding of aluminium and stainless steel we employ specially trained welders.
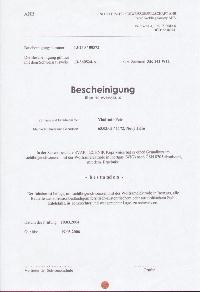
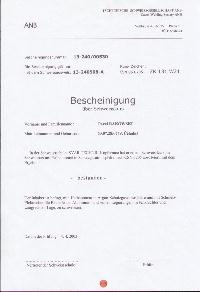
8. European Welding Expert DVS
Our welding specialist Wolfgang Müller was rewarded the DVS-diploma and he checks our production of welded parts according to DVS-guidelines (Deutscher Verein für Schweisstechnik).
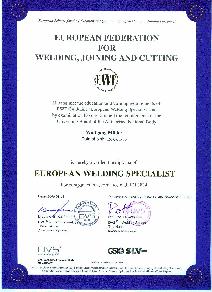
9. Material-certificates to EN 10204 3.1 and 3.2
We regularly deliver steel with certificates according to EN 10204 3.1 and 3.2 to customers with demanding applications:
- for example to customers from the public sector (Government of Germany), who order longterm investments into public transport systems
- for example to customers building heavy machinery (Schuler Presses) or heavy lifting equipment (HK), and who order these critical components from us.
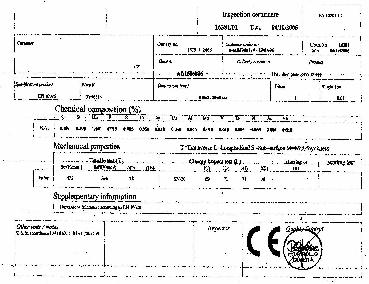
10. Laboratory-analysis
We can supply a laboratory analysis at short notice, that details the chemical composition and the mechanical properties of even very small samples, and thereby we have been able to check and document the correct material employed.
11. Hardness-measurements in Rockwell, Brinell and Vickers
We work with certified hardness-testing equipment to check the hardness of parts after receiving them from heat treatment and
in order to check structural changes after annealing. For the measurement of large parts we employ mobile testing equipment.
12. Penetration testing of welding seams
We regularly inspect the quality of our welding seams, using the red&white colour-penetration-test and we document the result.
13. Ultrasonic testing
We inspect the quality of castings and flame-cuts with ultrasonics according to EN 10160. Testing can be done before machining
on the rough flame-cut, as well as after machining on the final part. Ultrasonic testing is demanded by our customers for highly
stressed components.
14. Surface Roughness
We check surface roughness of milled or ground surfaces with a mobile surface roughness measuring apparatus, and thus we can
check and document directly all derived values like Ra, Rz, Rp, Rk, Rvk, etc., or we can check and classify surface roughness
according to the ISO-system with typical values in the range of ISO 5-10.
15. Paint thickness testing
Not only do we check the quality of painted parts by reference to agreed samples, but we also measure the thickness after the
primer and after final painting. This is especially important for machines and plants that are set up in open air. By reaching
and documenting the requested paint thickness we can guarantee the painted surface against corrosion for many years.
16. Leak-rate testing of vacuum components
We manufacture thin-walled and welded components for vacuum applications.
We check the leak-rate of these components with helium at leak-rates lower than 0,0001 bar.
17. Pressure testing of high-pressure components
We manufacture thin-walled and welded components for vacuum applications.
We can pressure-check these components currently up to 750 bar.
18. Customer specific quality measurements in assembly
With our customers for complete products we have defined additional measurements that check the correct function of delivered
tools or machines. This can be the measurement of the final closing distance of valves, or the parallel or vertical position of
assembled axes or drive trains. Thus our customers can deliver large tools or machines directly to Asia or South America with
documented quality.
19. X-Rax Analysis
An important quality issue of castings is the absence of all kinds of cavities. With our X-Ray chamber from Philips we can analyse many castings
and thus ascertain a top-quality.
20. Independent Quality Control
In large international projects, especially for bank-guarantees, it is often required to have the final quality checked additionally by external experts.
In our region there is a certified measuring company with the latest equipment, especially lasers, which carries out and certifies these measurements.
21. Competent employees and management
Most important of all are of course competent employees and workers, and a management that is keen on delivering top-quality products!